Perfume Zamac cap, also called zinc alloy cap, is heavy-touch and its exquisite and diverse shape bring the luxurious and upscale visual conflict for consumer. It is beloved by niche brands to embellish their exclusive perfume.
As the perfume caps mostly emphasize the uniqueness, the designs are usually stylish and complicated and therefore it is suitable for the die-casting method which needs to create the mold first and can mass produce and achieve the difficult structure in a cost-effective way accordingly. And Zamac exhibits an excellent combination of cost, strength, ductility, impact strength and finishing characteristics.They are the designer’s first choice when considering die casting.
Advantage of Zamac material
Zamac die castings offer excellent electroplating characteristics. Plating is the most popular decorative finish when corrosion and high abrasion resistance are required, which can be regularly done with gold,silver and rose gold. Polishing and brushing techniques can produce appearances similar to chrome plating or stainless steel. When lacquered, these finishes are suitable for decorative, interior applications. Besides,It can be riveting or clicking fitment between Zamac and PP instead of the regular glue. It can prevent the defects due to the glue when shipping in extremely weather,such as shipped from 30℃ to – 20℃.
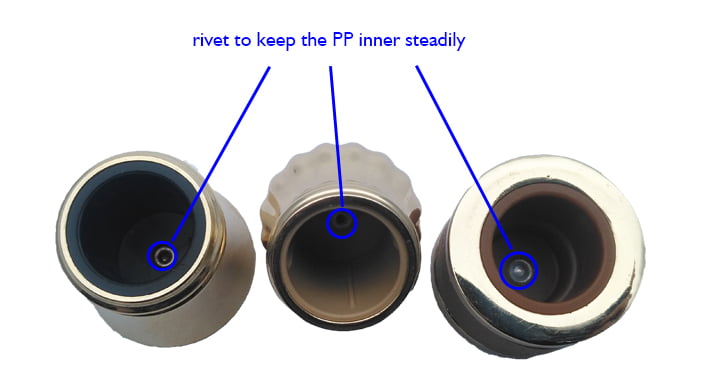
High purity material
For the Zamac material, it is very important to recognize and use the high purity Zamac. According to the Zamac die-casting history, a large problem with early Zamac die casting materials produced such as destructive environmental conditions and poor corrosion resistance owing to impurities in the alloys. It also remind us to choose the best quality Zamac material, and our Zamac chemical components comply with the American standard, the zinc content exceeds 95%, that ensure the high-quality Zamac cap from the raw material.
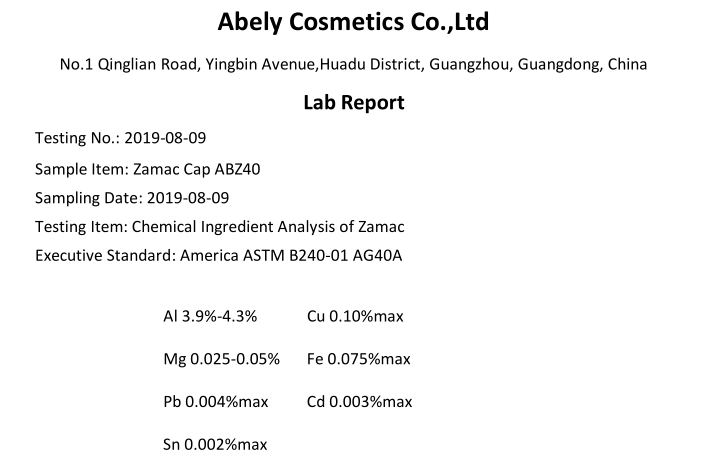
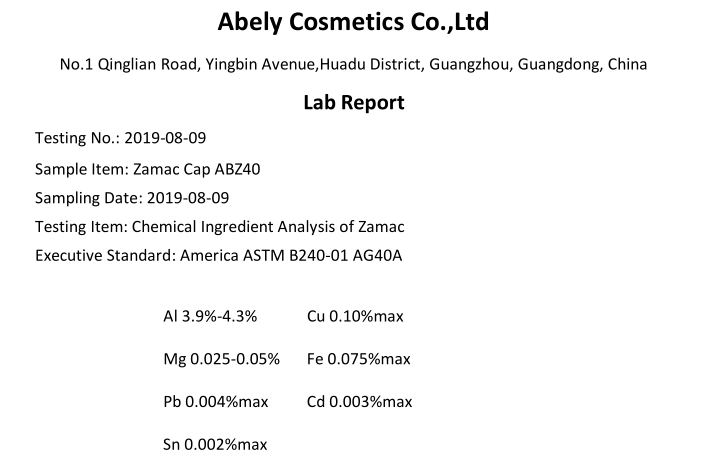
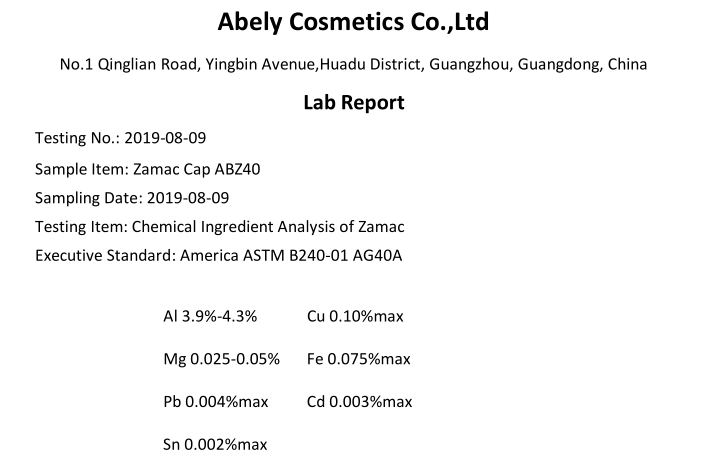
Processes of Zamac cap production
Different from plastic caps that produced by full automatic machines through injection mould, manual treatment occupies a large part in the production process of Zamac cap. The main processes: Die-casting mould – plain Zamac caps – removing cap holder – hand polishing surface – electroplating – assembly. For high-end market, the manual treatment takes longer time to keep every sides smoothly. One simple way to judge the quality of Zamac caps is to check the surface neatness and the thickness of electroplating film.
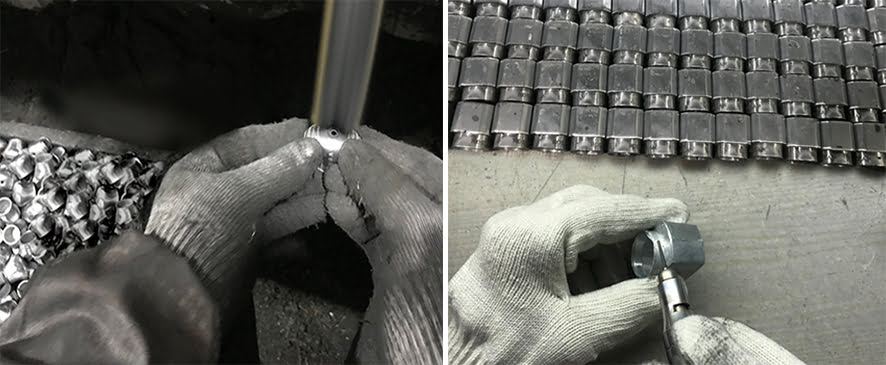
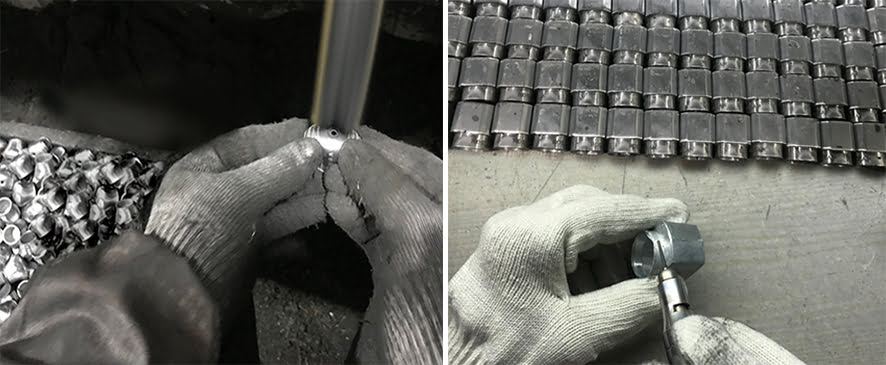
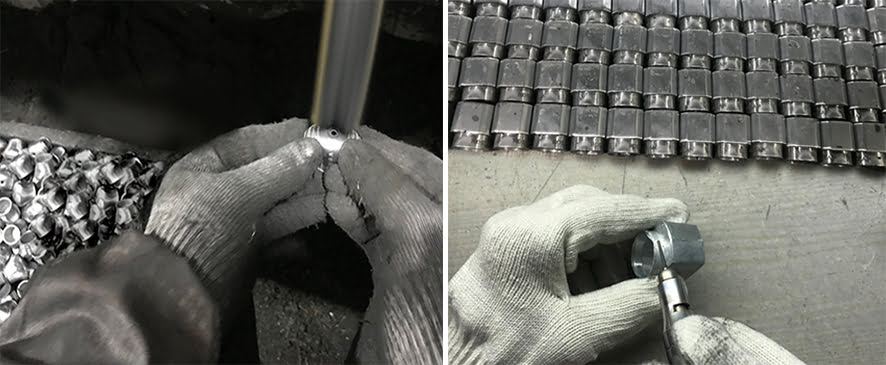
Inspection and Packaging for Zamac cap
We have a Stringent Quality System in place that guarantees your each perfume components, to be delivered with topnotch quality, and pass Strict Quality Inspection Standards. To make sure the quality, we do all kinds of testing before shipment, such as Salt Spray testing, Pull Testing, Adhesion Testing , Abrasion Testing, Perfume Resistance Testing. At the same time, we accept the 3rd part inspection, such as SGS, Asia Inspection, etc,.



Abely can provide you with high quality Zamac caps and we improve our services and technology of all aspects all the time to improve our customers’ satisfaction.To know about us, please do not hesitate to send an inquiry.